In today’s rapidly evolving technological landscape, digital transformation is no longer a luxury but a necessity for manufacturing companies aiming to stay competitive. The integration of advanced digital technologies into manufacturing processes not only enhances efficiency but also drives innovation, reduces costs, and improves overall productivity. This article will explore the pivotal strategies that are propelling digital transformation in manufacturing, ensuring businesses can navigate this complex terrain successfully.
Embracing Digital Transformation in Manufacturing
Digital transformation in manufacturing involves the adoption of cutting-edge technologies like the Internet of Things (IoT), Artificial Intelligence (AI), and big data analytics to revolutionize traditional manufacturing processes. The goal? To create smarter factories that are more efficient, flexible, and responsive to market demands. But how exactly can manufacturers embark on this transformative journey?
Understanding the Digital Transformation Landscape
The Importance of a Digital Strategy
Creating a robust digital strategy is the cornerstone of successful digital transformation. Without a well-defined plan, efforts can become disjointed and ineffective. A digital strategy should outline the goals, technologies to be adopted, and a roadmap for implementation.
Key Technologies Driving Transformation
Several key technologies are at the forefront of digital transformation in manufacturing. Here’s a closer look at a few of them:
- IoT (Internet of Things): IoT devices and sensors collect real-time data from manufacturing equipment and processes, enabling predictive maintenance and reducing downtime.
- AI and Machine Learning: These technologies help in analyzing vast amounts of data to optimize production processes, forecast demand, and improve quality control.
- Big Data Analytics: By harnessing big data, manufacturers can gain insights into their operations, identify trends, and make data-driven decisions.
- Cloud Computing: Cloud-based solutions provide scalability, flexibility, and real-time access to data, fostering collaboration and innovation.
- Robotics and Automation: Advanced robotics streamline manufacturing processes, increasing efficiency and reducing human error.
Strategies for Advancing Digital Transformation in Manufacturing
1. Start with a Clear Vision
Before diving into technology adoption, it’s crucial to have a clear vision of what you want to achieve with digital transformation. This vision should align with the company’s overall business goals and be communicated effectively across the organization.
2. Invest in Talent and Skills Development
Digital transformation requires a workforce skilled in new technologies. Investing in training and development programs ensures that employees are equipped to handle the challenges of a digitalized manufacturing environment.
3. Leverage Data to Drive Decisions
Data is the new oil in the digital age. Implementing systems that collect and analyze data can provide invaluable insights, driving smarter decision-making and optimizing operations.
4. Foster a Culture of Innovation
Encouraging a culture that embraces innovation and continuous improvement is essential. Employees should feel empowered to experiment with new ideas and technologies without fear of failure.
5. Implement Scalable Solutions
When selecting technologies, it’s important to choose solutions that can scale with the growth of your business. This ensures that your digital transformation efforts are sustainable in the long run.
6. Ensure Cybersecurity Measures
With increased connectivity comes increased risk. Robust cybersecurity measures must be in place to protect sensitive data and maintain the integrity of manufacturing processes.
7. Collaborate with Technology Partners
Partnering with technology providers and consultants can provide access to expertise and resources that might be lacking in-house. These partnerships can accelerate the implementation of digital transformation initiatives.
Images of Advancing Digital Transformation in Manufacturing: Key Strategies
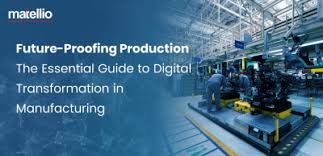
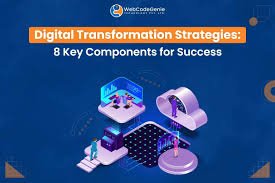
Overcoming Challenges in Digital Transformation
Resistance to Change
One of the biggest hurdles in digital transformation is resistance to change. Employees may be hesitant to adopt new technologies or alter their workflows. Addressing this through effective change management strategies is crucial.
High Initial Investment
The upfront cost of digital transformation can be significant. However, the long-term benefits in terms of efficiency gains and cost savings often justify the investment. Careful planning and phased implementation can help manage costs.
Integration with Legacy Systems
Integrating new digital solutions with existing legacy systems can be complex. It’s important to have a clear integration plan and possibly consider hybrid solutions that bridge the old and the new.
Real-World Examples of Digital Transformation in Manufacturing
Siemens’ Digital Factory
Siemens has been at the forefront of digital transformation with its Digital Factory initiative. By leveraging IoT, AI, and advanced robotics, Siemens has created a highly automated and interconnected manufacturing environment. This has resulted in significant improvements in production efficiency and product quality.
GE’s Brilliant Factory
General Electric (GE) has implemented the Brilliant Factory concept, utilizing big data analytics, machine learning, and advanced automation to create a smart manufacturing ecosystem. This initiative has enabled GE to optimize operations, reduce downtime, and enhance overall productivity.
FAQs
What is digital transformation in manufacturing?
Digital transformation in manufacturing involves integrating advanced digital technologies into traditional manufacturing processes to improve efficiency, innovation, and responsiveness.
Why is digital transformation important in manufacturing?
Digital transformation is crucial for staying competitive in a rapidly evolving market. It enhances efficiency, reduces costs, drives innovation, and improves product quality.
What are the key technologies in digital transformation?
Key technologies include IoT, AI, big data analytics, cloud computing, and advanced robotics.
How can manufacturers overcome resistance to change?
Effective change management strategies, clear communication of the benefits, and employee training can help overcome resistance to change.
What are the benefits of digital transformation in manufacturing?
Benefits include increased efficiency, cost savings, improved product quality, enhanced innovation, and better decision-making through data insights.
Conclusion
Advancing digital transformation in manufacturing is not just about adopting new technologies; it’s about rethinking processes, empowering employees, and creating a culture that embraces innovation. By implementing clear strategies, investing in talent, and leveraging the right technologies, manufacturers can navigate the complexities of digital transformation and position themselves for sustained success in the digital age.
Digital transformation is a journey, not a destination. As technology continues to evolve, so too must the strategies and approaches of manufacturers. Staying agile, continuously learning, and adapting to new trends will ensure that businesses not only survive but thrive in the ever-changing digital landscape.