In today’s fast-paced world, the manufacturing sector faces unprecedented challenges and opportunities. Technological advancements, globalization, and shifting consumer demands have revolutionized the industry. To stay ahead, companies must cultivate a culture of innovation that permeates every aspect of their operations. But what does this entail, and how can it be achieved? Let’s dive into the essential elements of building a culture of innovation in global manufacturing.
The Importance of Innovation in Manufacturing
Innovation isn’t just a buzzword; it’s the lifeblood of modern manufacturing. Companies that fail to innovate risk becoming obsolete, losing market share to more agile competitors. So, why is innovation so crucial?
Staying Competitive
The global manufacturing landscape is fiercely competitive. New players are constantly entering the market, bringing fresh ideas and technologies. To maintain a competitive edge, manufacturers must continuously innovate, improving processes, products, and services.
Meeting Consumer Demands
Consumers today expect more than ever before. They want high-quality products, personalized experiences, and sustainable practices. Innovation enables manufacturers to meet these demands, ensuring customer satisfaction and loyalty.
Driving Efficiency
Innovative practices can significantly enhance efficiency. Whether through automation, advanced analytics, or lean manufacturing principles, companies can streamline operations, reduce waste, and boost productivity.
Building a Culture of Innovation
Creating a culture of innovation is no small feat. It requires a strategic approach, involving leadership, collaboration, and a willingness to embrace change. Here’s a step-by-step guide to building a culture of innovation in global manufacturing.
1. Leadership Commitment
Innovation starts at the top. Leaders must demonstrate a clear commitment to fostering a culture of innovation. This involves setting a vision, allocating resources, and encouraging risk-taking.
Vision and Strategy
A compelling vision for innovation aligns the organization and provides direction. Leaders should articulate how innovation fits into the company’s broader goals and strategy.
Resource Allocation
Innovation requires investment. Leaders must ensure that sufficient resources—financial, human, and technological—are dedicated to innovation initiatives.
Encouraging Risk-Taking
Fear of failure can stifle innovation. Leaders should create an environment where taking calculated risks is encouraged and failure is seen as a learning opportunity.
2. Empowering Employees
Employees are the backbone of innovation. Empowering them to contribute ideas and drive change is crucial for building a culture of innovation.
Training and Development
Investing in employee training and development ensures that they have the skills and knowledge needed to innovate. This includes technical skills, problem-solving abilities, and creative thinking.
Open Communication
Encouraging open communication helps foster a culture of collaboration and idea-sharing. Employees should feel comfortable voicing their opinions and suggesting improvements.
Recognition and Rewards
Recognizing and rewarding innovative efforts reinforces their importance. This can include formal recognition programs, bonuses, or career advancement opportunities.
3. Fostering Collaboration
Innovation thrives in a collaborative environment. Encouraging cross-functional teamwork and external partnerships can lead to new ideas and solutions.
Cross-Functional Teams
Bringing together employees from different departments can spark creativity and innovation. Cross-functional teams can tackle complex problems from multiple angles, leading to more comprehensive solutions.
External Partnerships
Collaborating with external partners, such as suppliers, customers, and research institutions, can provide fresh perspectives and access to new technologies.
4. Leveraging Technology
Technology is a powerful enabler of innovation. Adopting the latest tools and technologies can drive efficiency, enhance product quality, and open new avenues for growth.
Automation and AI
Automation and artificial intelligence (AI) can transform manufacturing processes. From predictive maintenance to quality control, these technologies can improve efficiency and reduce errors.
Digital Twins
Digital twins—virtual replicas of physical assets—enable manufacturers to simulate and optimize processes. This can lead to significant improvements in product development and operational efficiency.
IoT and Data Analytics
The Internet of Things (IoT) and data analytics provide valuable insights into manufacturing operations. By analyzing data from connected devices, companies can identify areas for improvement and make data-driven decisions.
5. Cultivating a Learning Organization
A culture of continuous learning is essential for sustained innovation. Companies should encourage ongoing education and development to keep pace with changing technologies and market trends.
Continuous Improvement Programs
Implementing continuous improvement programs, such as Kaizen or Six Sigma, promotes a mindset of constant enhancement. These programs provide structured approaches to identifying and eliminating inefficiencies.
Knowledge Sharing
Encouraging knowledge sharing among employees helps disseminate best practices and lessons learned. This can be facilitated through internal workshops, online forums, and mentorship programs.
Staying Current
Keeping up with industry trends and emerging technologies is crucial. Companies should invest in market research, attend industry conferences, and subscribe to relevant publications.
Images of Building a Culture of Innovation in Global Manufacturing

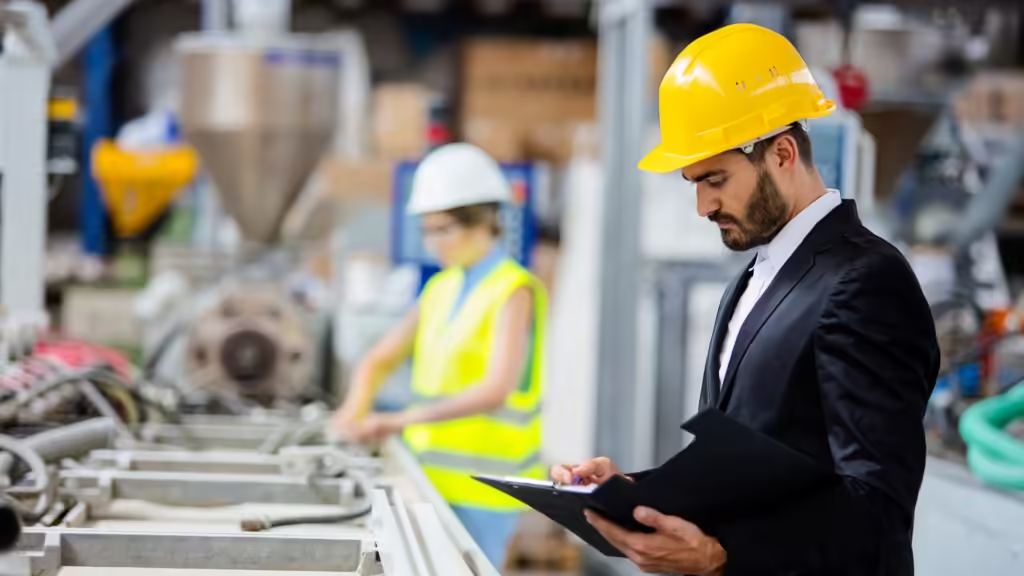
Overcoming Barriers to Innovation
Despite its importance, fostering innovation in manufacturing is not without challenges. Common barriers include resistance to change, limited resources, and regulatory constraints. Addressing these barriers is key to building a culture of innovation.
Resistance to Change
Change can be daunting, especially in established organizations. Overcoming resistance requires effective change management strategies, clear communication, and strong leadership.
Change Management
Implementing change management frameworks, such as Kotter’s 8-Step Process or ADKAR, can help guide organizations through transitions. These frameworks provide structured approaches to managing change and addressing resistance.
Clear Communication
Communicating the benefits of innovation and the rationale behind changes is essential. This helps build buy-in and reduces uncertainty.
Limited Resources
Innovation often requires significant investment. To overcome resource constraints, companies can seek external funding, form partnerships, or adopt incremental innovation approaches.
External Funding
Grants, venture capital, and government incentives can provide much-needed financial support for innovation initiatives.
Partnerships
Collaborating with other organizations can help share the burden of innovation costs and provide access to additional resources.
Incremental Innovation
Focusing on small, incremental improvements rather than large, disruptive changes can make innovation more manageable and cost-effective.
Regulatory Constraints
Regulatory requirements can pose significant challenges to innovation. Navigating these constraints requires a proactive approach and a thorough understanding of relevant regulations.
Proactive Compliance
Staying ahead of regulatory changes and proactively ensuring compliance can prevent costly setbacks. This involves regular audits, training, and collaboration with regulatory bodies.
Advocacy and Engagement
Engaging with industry associations and advocacy groups can help influence regulatory policies and promote a more innovation-friendly environment.
FAQs
Q: What is a culture of innovation in manufacturing? A: A culture of innovation in manufacturing is an environment where new ideas, processes, and technologies are continuously encouraged and integrated to improve efficiency, product quality, and competitiveness.
Q: Why is leadership important in fostering innovation? A: Leadership is crucial because it sets the vision, allocates resources, and creates an environment where risk-taking and creativity are encouraged.
Q: How can companies overcome resistance to change? A: Overcoming resistance requires effective change management strategies, clear communication, and strong leadership to build buy-in and reduce uncertainty.
Q: What role does technology play in manufacturing innovation? A: Technology is a key enabler of innovation, providing tools and capabilities that enhance efficiency, product quality, and the ability to respond to market demands.
Q: How can manufacturers stay current with industry trends? A: Manufacturers can stay current by investing in market research, attending industry conferences, subscribing to relevant publications, and fostering a culture of continuous learning.
Conclusion
Building a culture of innovation in global manufacturing is a multifaceted endeavor that requires commitment, collaboration, and a strategic approach. By fostering leadership commitment, empowering employees, encouraging collaboration, leveraging technology, and cultivating a learning organization, manufacturers can drive continuous improvement and maintain a competitive edge. Overcoming barriers such as resistance to change, limited resources, and regulatory constraints is crucial to sustaining innovation. Ultimately, companies that succeed in building a culture of innovation will be well-positioned to thrive in the dynamic and ever-evolving manufacturing landscap