In an era marked by rapid technological advancements, Industry 4.0 stands at the forefront of revolutionizing manufacturing. This fourth industrial revolution melds cutting-edge technologies with seamless connectivity, bringing forth an era where production processes are smarter, more efficient, and incredibly interconnected. From automation and data exchange to cyber-physical systems, Industry 4.0 is redefining the landscape of manufacturing, promising unparalleled enhancements in productivity and innovation.
The Genesis of Industry 4.0
The Evolution of Industrial Revolutions
To truly grasp the essence of Industry 4.0, it’s crucial to understand its historical context. The first industrial revolution, powered by steam engines and mechanized production, laid the groundwork for mass manufacturing. The second wave, marked by electrical power and assembly lines, further streamlined production processes. The third revolution, characterized by the advent of computers and automation, brought unprecedented efficiency to manufacturing. Now, Industry 4.0, with its emphasis on connectivity and smart technology, is set to redefine the very nature of industrial production.
Defining Industry 4.0
So, what exactly is Industry 4.0? At its core, Industry 4.0 refers to the integration of digital technologies into manufacturing, creating a “smart factory” environment. It’s all about connecting machines, systems, and humans in real-time to enhance productivity, efficiency, and flexibility. This revolution leverages the Internet of Things (IoT), artificial intelligence (AI), big data, and cloud computing to create a seamless and intelligent production ecosystem.
The Pillars of Industry 4.0
The Internet of Things (IoT)
One of the cornerstones of Industry 4.0 is the Internet of Things (IoT). IoT connects machines, devices, and sensors, enabling them to communicate and share data. In a manufacturing setting, this connectivity allows for real-time monitoring and control of production processes. For instance, smart sensors can track machine performance, predict maintenance needs, and optimize production schedules, reducing downtime and increasing efficiency.
Big Data and Analytics
In the realm of Industry 4.0, data is the new gold. With the proliferation of IoT devices, vast amounts of data are generated every second. Big data analytics plays a pivotal role in making sense of this data, uncovering patterns, and providing actionable insights. By analyzing production data, manufacturers can identify bottlenecks, optimize resource allocation, and enhance product quality. Predictive analytics, powered by AI, enables proactive decision-making, ensuring that potential issues are addressed before they escalate.
Cyber-Physical Systems (CPS)
Cyber-physical systems (CPS) are integral to the concept of Industry 4.0. These systems integrate physical processes with digital technology, creating a seamless interaction between the virtual and real worlds. In a smart factory, CPS enables machines to make autonomous decisions, adapt to changing conditions, and collaborate with other systems. For example, robotic arms equipped with AI can work alongside human operators, enhancing precision and productivity.
Cloud Computing
Cloud computing serves as the backbone of Industry 4.0, providing the infrastructure needed to store, process, and analyze vast amounts of data. With cloud-based platforms, manufacturers can access data and applications from anywhere, facilitating collaboration and innovation. Cloud computing also ensures scalability, allowing companies to expand their operations without significant upfront investments in IT infrastructure.
Artificial Intelligence (AI) and Machine Learning
Artificial intelligence and machine learning are driving forces behind the intelligent automation of Industry 4.0. AI algorithms can analyze data, learn from it, and make informed decisions. Machine learning, a subset of AI, enables systems to improve their performance over time by learning from experience. In manufacturing, AI-powered systems can optimize production processes, enhance quality control, and predict equipment failures, minimizing downtime and maximizing efficiency.
Transformative Benefits of Industry 4.0
Enhanced Efficiency and Productivity
One of the most significant benefits of Industry 4.0 is the substantial boost in efficiency and productivity. With real-time data and intelligent automation, manufacturers can streamline their operations, reduce waste, and optimize resource utilization. Smart factories can operate 24/7, with minimal human intervention, ensuring continuous production and faster turnaround times.
Improved Quality Control
Quality control is a critical aspect of manufacturing, and Industry 4.0 takes it to the next level. Advanced sensors and AI-powered inspection systems can detect defects with high precision, ensuring that only top-quality products reach the market. Real-time monitoring allows for immediate corrective actions, reducing the likelihood of defective products and enhancing customer satisfaction.
Flexibility and Customization
In today’s dynamic market, the ability to adapt quickly to changing demands is crucial. Industry 4.0 enables manufacturers to achieve high levels of flexibility and customization. With reconfigurable production lines and smart machines, companies can swiftly switch between different products and respond to customer preferences. Mass customization, where products are tailored to individual specifications, becomes a reality, offering a competitive edge.
Predictive Maintenance
Traditional maintenance practices are often reactive, addressing issues only after they occur. Industry 4.0 introduces predictive maintenance, where AI algorithms analyze data from machines to predict potential failures. By addressing issues before they escalate, manufacturers can reduce downtime, extend the lifespan of equipment, and save on maintenance costs.
Supply Chain Optimization
A connected and intelligent manufacturing ecosystem extends beyond the factory floor to the entire supply chain. Industry 4.0 enhances supply chain visibility, enabling real-time tracking of materials, products, and shipments. This visibility allows for better inventory management, reduced lead times, and improved coordination with suppliers and distributors.
Overcoming Challenges in Industry 4.0 Adoption
Data Security and Privacy
With increased connectivity comes the challenge of data security and privacy. The vast amount of data generated and shared in an Industry 4.0 environment must be protected from cyber threats. Manufacturers need to implement robust cybersecurity measures, including encryption, access controls, and regular security audits, to safeguard sensitive information.
Workforce Transformation
The shift to Industry 4.0 requires a transformation of the workforce. As automation and AI take over repetitive tasks, there is a growing demand for skilled workers who can manage and maintain these advanced systems. Companies must invest in training and upskilling their employees, ensuring they have the necessary expertise to thrive in a smart manufacturing environment.
Integration Complexity
Integrating legacy systems with new technologies can be a complex and challenging process. Many manufacturers have existing infrastructure that may not be compatible with Industry 4.0 solutions. To overcome this challenge, companies should adopt a phased approach, gradually integrating new technologies while ensuring seamless interoperability with existing systems.
Image of Industry 4.0: Revolutionizing Manufacturing with Connectivity
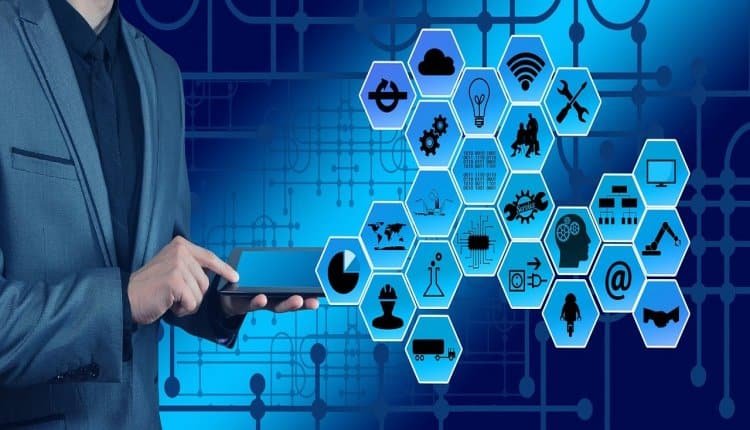
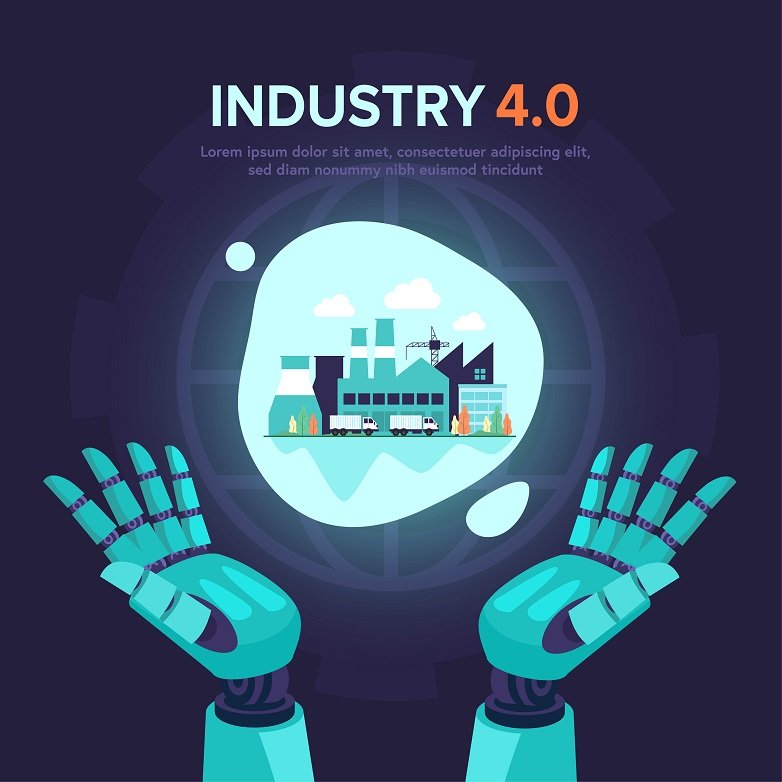
FAQs About Industry 4.0
What is Industry 4.0?
Industry 4.0 refers to the fourth industrial revolution, characterized by the integration of digital technologies and connectivity into manufacturing processes, creating smart factories and enhancing efficiency and productivity.
How does IoT contribute to Industry 4.0?
The Internet of Things (IoT) connects machines, devices, and sensors, enabling real-time communication and data exchange. In Industry 4.0, IoT allows for real-time monitoring, predictive maintenance, and optimization of production processes.
What are the benefits of Industry 4.0 for manufacturers?
Industry 4.0 offers numerous benefits, including enhanced efficiency and productivity, improved quality control, flexibility and customization, predictive maintenance, and supply chain optimization.
What challenges do manufacturers face in adopting Industry 4.0?
Manufacturers face challenges such as data security and privacy concerns, the need for workforce transformation, and the complexity of integrating new technologies with existing systems.
How can manufacturers overcome the challenges of Industry 4.0 adoption?
To overcome these challenges, manufacturers should implement robust cybersecurity measures, invest in workforce training and upskilling, and adopt a phased approach to integrating new technologies with existing systems.
Conclusion
Industry 4.0 is not just a technological evolution; it’s a transformative journey that’s reshaping the manufacturing landscape. By leveraging advanced connectivity, smart technologies, and integrated systems, manufacturers can achieve unprecedented levels of efficiency, productivity, and innovation. As companies navigate the challenges of this new era, the potential rewards are immense, paving the way for a future where manufacturing is more intelligent, responsive, and sustainable than ever before. Embracing Industry 4.0 means embracing the future of manufacturing—a future defined by connectivity and limitless possibilities.