Injection molding, a pivotal manufacturing process, has steadily revolutionized industries across the globe, and India is no exception. From automotive components to medical devices, this technique has become the backbone of many manufacturing sectors. In this comprehensive exploration, we delve into the intricacies of injection molding in India, examining its applications, benefits, and the challenges it faces, along with a glimpse into its promising future.
The Essence of Injection Molding
What is Injection Molding?
Injection molding is a manufacturing process used for producing parts by injecting molten material into a mold. It is predominantly used with thermoplastic and thermosetting polymers, which, once heated, can be shaped and cooled to form the desired product.
How Does It Work?
The process involves several steps:
- Material Preparation: The plastic granules are fed into a heated barrel, where they melt and become pliable.
- Injection: The molten material is then injected into a mold cavity under high pressure.
- Cooling: The mold is cooled, allowing the material to solidify into the desired shape.
- Ejection: The finished part is ejected from the mold.
Injection Molding in India: A Growing Industry
Historical Perspective
The journey of injection molding in India began in the late 20th century, initially driven by the automotive and consumer goods sectors. Over the years, advancements in technology and an increasing demand for high-quality products have fueled its growth, making it an integral part of the Indian manufacturing landscape.
Current Market Scenario
Today, injection molding in India stands as a robust industry with a diverse range of applications. According to recent reports, the Indian injection molding market is poised to grow significantly, driven by the booming automotive, electronics, and medical industries. The availability of skilled labor, cost-effective production, and a growing domestic market contribute to this upward trajectory.
Applications of Injection Molding in India
Automotive Industry
India’s automotive sector has witnessed exponential growth, and injection molding plays a crucial role in this expansion. Components such as dashboards, bumpers, and various engine parts are produced using this technique, ensuring precision and durability.
Consumer Goods
From everyday household items to complex electronic devices, injection molding is at the heart of the consumer goods industry. This process allows for the mass production of high-quality products at an affordable cost, catering to the diverse needs of the Indian population.
Medical Devices
In the medical field, precision and reliability are paramount. Injection molding is extensively used to manufacture medical devices such as syringes, surgical instruments, and even components for diagnostic equipment. The ability to produce sterile and precise parts makes it indispensable in this sector.
Electronics
With the rise of the electronics industry in India, injection molding has become a go-to method for producing components like connectors, housings, and other intricate parts. The precision and efficiency offered by this process are critical in meeting the high standards of electronic products.
Image of Injection molding in india
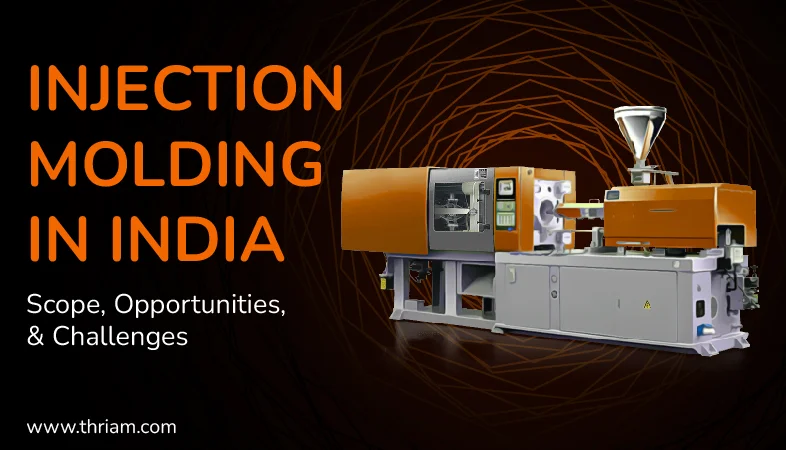
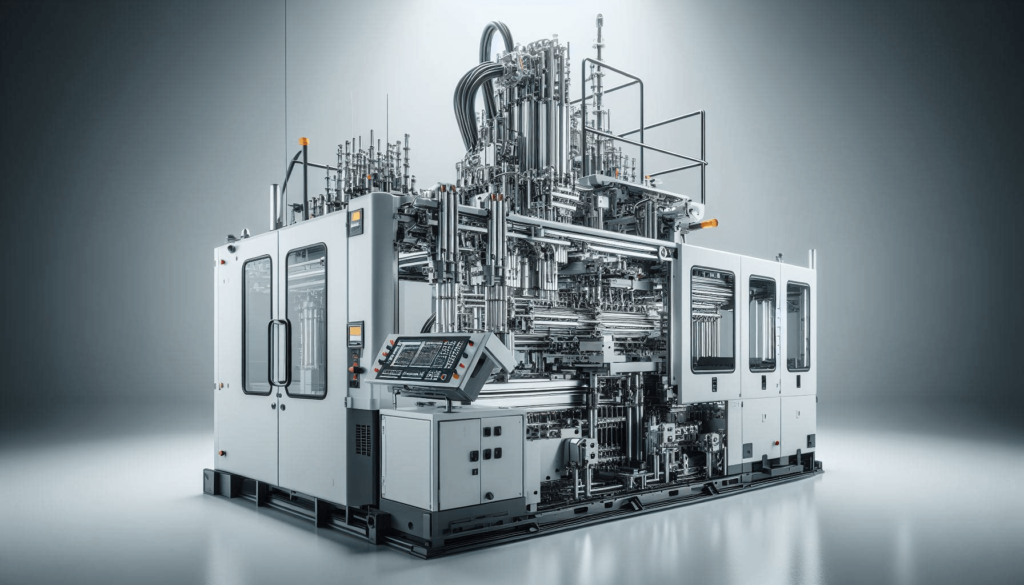
Benefits of Injection Molding
High Efficiency and Production Rate
One of the primary advantages of injection molding is its high efficiency. Once the initial setup is complete, the process allows for the rapid production of large quantities of parts with minimal labor intervention.
Design Flexibility
Injection molding offers immense design flexibility. Complex geometries and detailed features can be easily incorporated into the mold, allowing for the creation of intricate parts that would be challenging to produce using other methods.
Material Versatility
A wide range of materials can be used in injection molding, from various types of plastics to metals and ceramics. This versatility makes it suitable for producing parts for diverse applications.
Cost-Effective Production
Despite the initial setup costs, injection molding becomes highly cost-effective in the long run, especially for large production runs. The ability to produce high volumes at a low per-unit cost is a significant advantage.
Challenges Facing the Injection Molding Industry in India
High Initial Investment
The initial investment required for setting up injection molding facilities can be substantial. This includes the cost of machinery, molds, and other ancillary equipment, which can be a barrier for small and medium-sized enterprises.
Skilled Labor Shortage
While India boasts a large workforce, the availability of skilled labor specific to injection molding is limited. This shortage can lead to inefficiencies and quality issues in production.
Technological Advancements
Keeping pace with rapid technological advancements is another challenge. The injection molding industry needs continuous investment in research and development to stay competitive and meet evolving market demands.
Environmental Concerns
The environmental impact of plastic waste is a significant concern. The industry must adopt sustainable practices and explore alternatives such as biodegradable materials to mitigate its environmental footprint.
Future Prospects of Injection Molding in India
Technological Innovations
The future of injection molding in India looks promising, with advancements in technology paving the way for more efficient and sustainable practices. Innovations such as 3D printing and automation are expected to complement traditional injection molding, enhancing productivity and precision.
Growing Domestic and International Demand
As India’s manufacturing capabilities continue to grow, the demand for injection molded products is set to rise. The expanding domestic market, coupled with increasing exports, presents a significant opportunity for the industry.
Government Initiatives
The Indian government’s focus on boosting manufacturing through initiatives like “Make in India” provides a conducive environment for the growth of injection molding. Policies aimed at enhancing infrastructure, providing financial incentives, and promoting skill development will further bolster the industry.
FAQs
What materials are commonly used in injection molding?
Materials commonly used include thermoplastics (such as polyethylene, polystyrene, and polyvinyl chloride), thermosetting polymers, and certain metals and ceramics.
How long does the injection molding process take?
The cycle time for injection molding can vary from a few seconds to several minutes, depending on the complexity of the part and the material used.
Is injection molding environmentally friendly?
While traditional injection molding has an environmental impact due to plastic waste, the industry is increasingly adopting sustainable practices, such as using recycled materials and developing biodegradable polymers.
What are the typical applications of injection molding in the medical industry?
Injection molding is used to produce a variety of medical devices, including syringes, surgical instruments, diagnostic equipment components, and implantable devices.
Conclusion
Injection molding in India has evolved into a dynamic and essential industry, playing a pivotal role in the manufacturing sector. Its applications span across various fields, offering numerous benefits such as high efficiency, design flexibility, and cost-effective production. However, the industry also faces challenges that need to be addressed to ensure sustained growth. With continuous technological advancements, supportive government policies, and a focus on sustainability, the future of injection molding in India appears bright, promising continued innovation and expansion.